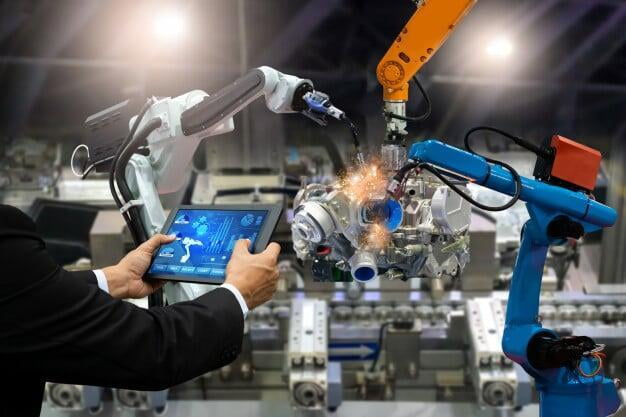
The ongoing discourse on advanced manufacturing technologies during the COVID19 pandemic has shone light on the fact we have entered the era of complete digitization. Overnight, governments, business, health care providers, even educational institutions have moved their operations online. As citizens and consumers, we are slowly growing accustomed to new levels of tele-working and tele-communications, and have found new ways of enhancing efficiency in the digital realm.
India is Ready for the Successful Transition to Digitization
Recently, the United Nations Industrial Development Organization (UNIDO) brought out its flagship Industrial Development report on Industrialization in the digital age. The report provides key insights on the development, application and implementation of Advanced Digital Production (ADP) technologies, now commonly referred to as Industry 4,0 technologies – from the perspective of developing countries.
Of these, India is the single lower-to-middle-income nation that has been categorized with a group of secondary economies well-poised for a complete digital transformation by successfully leveraging these technologies.
A number of Indian manufacturing firms have also made the transition to Industry 4.0 technologies, though they are still, by far, outnumbered by those that continue to operate with relatively rudimentary instrumentation and controls. One major hurdle getting in the way is the lack of successful, integrated training programs that cover the spectrum of functions related to successful deployment of ADP technologies.
Industry 4.0 is Changing the Fabric of Manufacturing Processes
UNIDO has also presented factual evidence to support the claim that Industry 4.0 can facilitate an inclusive and sustainable mode of industrial development. ADP-enabled product and market innovations offer superior productivity, quality, market-responsiveness and client customization. Furthermore, factories can benefit immensely from improved monitoring and predictive maintenance, enabling them to save energy and function economically.
Industry 4.0 technologies have largely blurred the boundaries between physical and digital, successfully combining hardware, software, and connectivity. This is a transformational opportunity, generally captured as the fourth industrial revolution, or IR4. Applied to manufacturing this results in smart factories.
Where Training Comes in
In today’s changing world, where we’re headed towards complete digitization, there is likely to be fewer jobs on the shop floor, yet more opportunities in knowledge-intensive areas and functions that are needed to leverage Industry 4.0 technologies.
This workforce transition calls for careful consideration, efficient planning and management towards positive outcomes. Industrial skills geared towards the future of technology implementation will be a game-changer; they include analytical skills, specific technology-related skills – on both advanced digital and new physical technologies- and soft skills, with an emphasis on collaboration. Therefore, a successful blend of industrial capabilities with in-depth knowledge of digital and physical technologies is imperative.
E-Learning is Paving the Way for Successful, Integrated Training
E-Learning has facilitated new modes of skill-development that were previously not possible, for leveraging new technologies. Today, you are presented with the opportunity to cover several aspects of Industry 4.0 at once, covering different subjects within its scope and across different levels of study – all with the flexibility of self-study. In short, you learn more efficiently when you learn at a pace that you find comfortable.
A great advantage of E-Learning is its facility to synthesize the classroom and online mode of study into a single concept known as ‘Blended Learning’. With successful blended learning in place, you get to reap the benefits of self-study without compromising on the rigour of face-to-face, interactive learning.
An employee of an organization may choose to narrow his focus and specialise in specific areas with the objective of aligning his study with the larger goals of the organization; by enabling this process and even making it an integral part of employee-training, the latter takes a positive leap forward with regard to bridging the gaps in Industry 4.0 implementation.
MTC is your trusted e-learning partner for advanced manufacturing technologies (AMT) – we are committed to facilitating industry-relevant training for institutions and enterprises, offering end users an interactive E-Learning platform.
As thought-leaders in modern factory technologies, we bring you a range of essential course material that will help empower your employees to equip themselves with the skills to handle today’s dynamic technological environment.
Successfully navigating the current digital transformation requires a unique blend of skill development and application – this forms the foundation of our interactive platform: get in touch with us at MTC and gain access to our extensive digital library of E-Learning content.