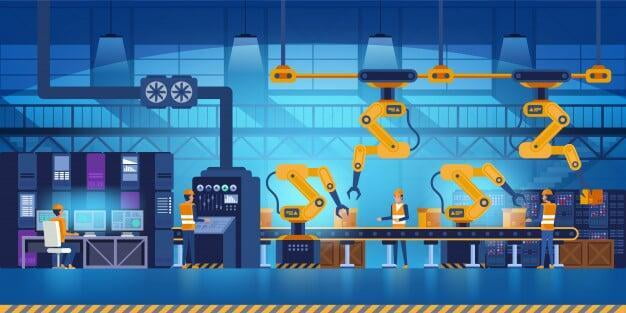
The Internet of Things has completely broken down barriers in various industries. This transformative quality of IoT is all the more pronounced in Manufacturing, carrying with it a capability to introduce dynamic and interconnected systems of operations and monitoring in the place of traditionally linear ones.
To facilitate IoT and industrial IoT, manufacturing facilities have got to embrace complete wireless connectivity and the technologies that support it. Seamless IoT transformation calls for low power and long range, addressed by the Narrowband (NB) standard. NB connections support a wide range of IoT processes, including smart detectors, event detectors, smart garbage bins, asset tracking, machine monitoring, and a host of other applications.
Radical Changes that are Inevitable Thanks to IoT
Radical Changes that are Inevitable Thanks to IoT
The changes made possible by IoT are systemic – they work across processes and levels, providing every manufacturing concern the opportunity to radically transform the core of their operations and accelerate their growth.
What are the inevitable results of embracing IoT in Manufacturing?
- Enhanced visibility of Production Assets and Processes
With IoT and Industrial IoT, manufacturers can connect the tools and assets in factories and warehouses with essential production equipment and machines, each and all of them running through new technologies that enable efficient tracking and monitoring.
IoT provides engineers a high level of visibility into production operations and the ability to foresee the arrival of issues that may disrupt them. A critical capability of IoT is that it can facilitate ‘Asset Tracking’ – a system to easily locate, track, and monitor essential components of a production facility.
Manufacturing concerns are empowered with the ability to automatically track parts as they move through the assembly process, with the help of smart sensors. Plant managers gain real-time access to production output figures through the connection of operating tools with the machines.
Manufacturers can now leverage the high levels of real-time visibility within plants to identify, understand, and resolve problems through the use of dashboards with IoT-generated data. This brings them faster, more efficient, more accurate, and higher quality production.
- Predictive Maintenance
A major priority of manufacturers is ensuring that assets and factory equipment are in working condition and function smoothly. A single malfunction can disrupt production, which in turn, can cause losses due to unexpected costs on equipment replacement or replacement; more critically, it can lead to delays or cancellations of orders, causing customers’ trust to be breached.
The continual running of machines can help reduce operating expenses and smoothen processes in production. By connecting wireless sensors lodged on all the machines to the internet, managers gain real-time access and visibility to performance, being able to detect early signs of malfunction well before they occur. Moreover, manufacturers benefit immensely from the leveraging of such capabilities towards safer environments and increased equipment life cycles within plants.
- Improved Product Quality
With continuous monitoring of products through the building cycle in place through the use of environmental sensors, manufacturers are empowered with the ability to ensure that their products always meet a high standard of quality. The environmental sensors send back critical back data about conditions of the products, enabling a streamlined monitoring system.
The use of the digital twin greatly enhances performance analysis. Feedback on various processes are analyzed and provided as input into the product design and process design, which in turn enables continual optimization.
- Optimized Supply Chain Management
Manufacturers are seeing supply chain processes grow increasingly complex as they begin to expand their operations on a global scale. IoT allows concerns to monitor critical events across their supply chain processes, bringing them real-time data that tracks assets like trucks, containers, and individual products.
Wireless sensors track and monitor inventories while they move from one location to another in the supply chain, including shipments of supplies for products, right through to the delivery of products in their finished form. Manufacturers gain enhanced visibility into product inventories, having more accurate schedules for material availability, as well as for the shipment of products to customers. Analysis of critical data helps manufacturing enterprises make vast logical improvements by identifying problem areas and resolving them
- Leveraging Digital Twin
Put very simply, Digital Twins are virtual replicas of physical devices, products, and processes, that manufacturers can use to run simulations before they go ahead with actually building and deploying them.
Using perpetual streams of real-time data made possible by IoT, manufacturers can now create a digital twin of any type of product, and at any level, irrespective of what features define it. They can detect bottlenecks sooner and predict outcomes accurately, giving them the opportunity to produce only high quality products that meet their standard, as well enabling them to reduce costs that are normally spent on tracking and recalling products once they are shopped.
Data collected from digital replicas also lets managers analyze the performance of systems under various conditions on-field.
Thus, with a spectrum of potential applications at a manufacturer’s disposal, the five cases for IoT’s potential that we explored could revolutionize Manufacturing as a whole. In order to realize this idea, however, adequate training is required across the board.
MTC is your trusted e-learning partner for IoT, Industry 4.0, and advanced manufacturing technologies (AMT) – we are committed to facilitating industry-relevant training for institutions and enterprises, offering end users an interactive E-Learning platform.
As thought-leaders in modern factory technologies, we bring you a range of rich digital learning content that will help empower your employees to equip themselves with the skills to handle today’s dynamic technological environment.
Successfully navigating the IoT revolution in Manufacturing requires a unique blend of skill development and application – this forms the foundation of our interactive platform: get in touch with us at MTC and gain access to our extensive digital library of E-Learning content.